Choose The Right Grease
The proper grease application to machine components regularly exposed to water and other contaminants is essential to maintaining forestry equipment. Grease acts as both a lubricant and sealant to protect components such as bearings, universal joints and pins and bushings against wear, dust, water and other work-site contaminants. It is composed of a base oil, a thickener, and additives that provide specific anti-wear and anti-corrosion protection.
An essential grease specification is its NLGI (National Lubrication Grease Institute) grade, which measures thickness or “stiffness.” The NLGI grading scale begins with No. 000, only slightly thicker than motor oil, and gets progressively thicker from 00, 0, 1, – up to 6, which is a solid lubricant.
The most common and versatile grade used in forestry equipment is No. 2, with a consistency akin to paste car wax or cake frosting. John Deere applies a multipurpose, polyurea-thickened, No. 2 grease for initial lubrication on all axle bearings, U-joints and articulations of its forestry equipment.
Match Grease
Choosing the right grease for a machine component depends on the equipment itself, the application of the equipment, and the specific working conditions to which the equipment is subjected.
As with most maintenance decisions, it’s generally best to follow the recommendations of the equipment manufacturer, your dealer or your fuel/fluids supplier. A multipurpose No. 2 grease is widely recommended for most bearings and joints, and in most cases, there’s no need to waste money on higher-priced, higher-performance products. However, a lightweight, high performance grease may be recommended for high-velocity CV joints in drive shafts, gearboxes or other sealed components. A heavy grease may also be needed for large, open joints, and synthetic grease may be required for extreme temperature conditions or where the application itself generates high heat.
For wet applications in swampy areas, logging equipment requires grease that protects against rust and won’t be easily washed out by extended exposure to water. Viable grease options for such conditions include calcium-based, aluminum-based, polyurea-based or even lithium-based greases. These greases repel water well, protect against corrosion and do not wash easily under wet environments.
Use the product that’s blended and priced right for your needs. You don’t need a high-temperature grease, for example, if you don’t have a high-temperature application. If a grease is working well for your particular equipment, application and conditions, stick with it. Switching can cause problems because mixing greases with different bases or thickeners can degrade the properties of both the original and the new grease. If you must switch, your dealer or supplier can refer to manufacturers’ compatibility charts to help ensure different greases can work properly together.
Finally, be sure you apply any grease properly. Follow your equipment manufacturer’s recommendations for application intervals (typically daily, 100, 500 to 1,000 hours) and for the amount of grease you apply to each component. Be careful not to exceed the manufacturer’s specified amount for each component. Too much grease can burst seals, ruin bearings or otherwise contaminate the ground or water.
Latest News

IP Closure Announcement Continues Market Shift
The pulp and paper industry continues its painful supply side market shift as officials with International Paper in late October announced the company will permanently close its containerboard mill in Orange, Tex., and will permanently cease…
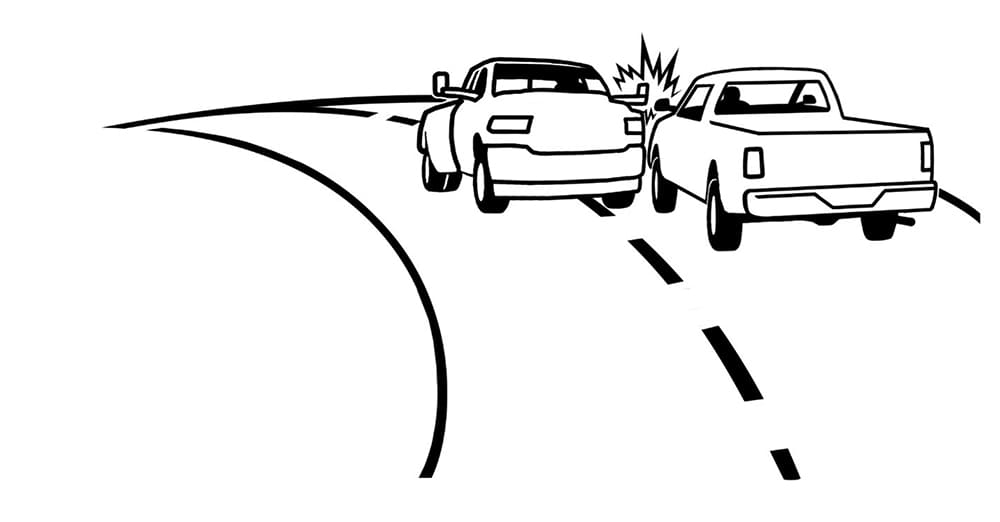
Driver Injured By Side Mirror Impact With Oncoming Truck
BACKGROUND: It was a clear winter morning in the Southeastern U.S. A logging company pickup truck was traveling to the job site around dawn. PERSONAL CHARACTERISTICS: The logging company pickup truck’s side mirror was struck by the extended mirror…
Have A Question?
Send Us A Message