Contaminants: Water, Air, Sludge
In hydraulic oil, typically less than 0.1% water is considered excessive. Water can slow the filtering process; react with additives in the oil to produce other contaminants or acids; and reduce the lubricating effectiveness of fluid. Less lubrication, or lower viscosity, means that components are more likely to experience metal-to-metal contact, producing metal shavings.
Air is always in a hydraulic system, but too much air can react with additives in the oil to produce other contaminants or acids; produce foam, reducing lubrication; cause controls to feel less responsive or less powerful; and dissolve in the oil, then develop into bubbles in low pressure areas. When bubbles collapse in higher pressure areas, component damage and noise can occur.
Sludge is a thick substance that can be created by the reaction of water or air and other contaminants, referred to as oxidation—the amount of oxidation in a fluid doubles with every 10°C change in temperature. It can plug filters, orifices and small passages; prevent enough oil from flowing to the pump, causing cavitation, which is severe damage in the pump; and cause erratic functions.
These types of contamination are as serious financially as particle contamination. If contamination is allowed to build in the system filters will have to be replaced more often; components may fail; productivity and downtime will increase; and the system may need to be flushed.
Water can enter the system anytime a component is opened or replaced, through the reservoir access plate or during hose replacements. Air can enter the system through leaks, especially at the pump inlet, and by splashing in the reservoir. Sludge is typically a result of contaminants already in the system reacting with the oil or other contaminants.
Preventing Contamination
Although this is not a comprehensive list, adhering to these guidelines will reduce downtime, component replacement costs and other costs associated with contamination:
Ensure that anti-oxidants, defoaming additives and other additives in the oil meet manufacturer specifications. These should be listed in the machine manuals.
Prevent air leaks in hydraulic hoses and components, especially at the pump inlet.
Larger hydraulic oil tanks can allow these contaminants to settle, thus cleansing the system. They also keep the oil temperature lower, which prevents the creation of some types of contamination such as oxidation.
Test your hydraulic fluid for contamination on a regular basis, especially if only one type of oil is used throughout the year.
Submitted by the Forest Machine Business Dept., Komatsu America Corp.
Latest News
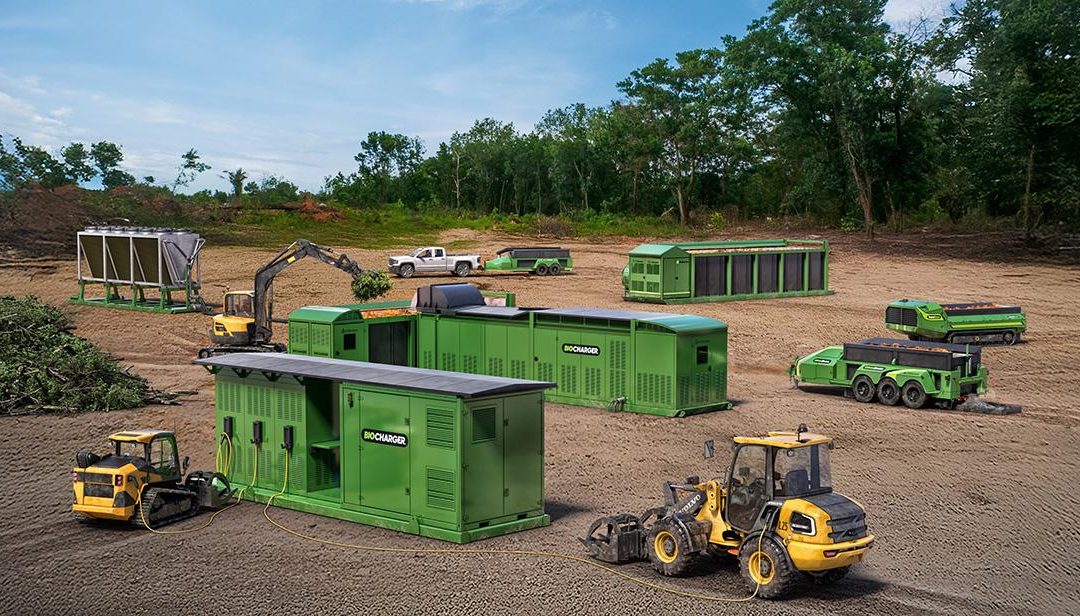
BioCharger, CharBoss From AirBurners Available For Demos
Air Burners is the world’s leading manufacturer of Air Curtain Burner Systems, offering the most economical and environmentally friendly solution for vegetative waste disposal. With decades of expertise, Air Burners has developed rugged, reliable...
Tennessee Announces New State Forest
The Tennessee Department of Agriculture, Division of Forestry (TDF) has announced that 5,477 acres in Fayette County will become the state’s 16th state forest, which will be named Wolf River State Forest. “This property holds great historical,...
Have A Question?
Send Us A Message