Down & Dirty, Part 1
In the world of “clean,” particle size is defined in microns, an ideal measurement used for measuring things smaller than the naked eye can see. A micron (µ), short for micrometer, is a metric unit of measurement equal to one millionth of a meter or about 4 hundred thousandths of an inch (0.00004”). To help put this in perspective, the period used to end this sentence is about 397 microns in diameter. The eye of a needle used to stitch a child’s pants would be around 749 microns wide, a human hair 40 to 120 microns in diameter, and a stamp more than 25,000 microns on a side.
Here are some examples of “particles” and their sizes: Grain of table salt, 100 µ; human hair diameter, 70 µ; limit of visibility, 40 µ; white blood cell, 25 µ; red blood cell, 8 µ; bacteria, 2 µ.
Hydraulic filters used on modern heavy equipment are typically designed to remove particles between 7-10 µ. Examples are dirt, metal shavings, seal material, etc. If we ran human blood through the same filters, they would actually remove the white blood cells!
The International Organization for Standardization (ISO) created the cleanliness code 4406:1999 to quantify particulate contamination levels per milliliter of fluid. This code defines cleanliness in terms of the number of particles per unit volume greater than 4, 6 and 14 µ, respectively. The code is expressed in three numbers; the lower the ISO code rating, the cleaner the oil. For example a rating of 16/14/11 is much cleaner than 17/14/13. Because most of the particles are too small for the naked eye to see, it is difficult to use the ISO Code rating unless it references test results such as oil sample analyses.
Particle Invasion
There are many culprits. Some of the most common avenues of contamination are:
Adding unfiltered oil directly to the hydraulic tank; Operating with high hydraulic oil temperatures (heat causes hoses, seals or other components to degenerate and contaminate oil); Using low viscosity oils. Thin oils have reduced lubrication capability. Thin oil films increase the chances for metal-to-metal contact and resulting metallic shavings/particles entering the oil stream; Normal component wear over time; Replacing components in a dirty environment; Using hoses that have not been properly cleaned after assembly. Using dirty hoses is one of the easiest ways to ensure component failure.
Particles Damage
A multitude of issues on the machine can be attributed to contamination, only a few of which are discussed here. Machines today frequently use piston pumps and motors operating at very high pressures. These precision components are manufactured with very tight tolerances for high performance and efficiency. The tighter these tolerances become, the more susceptible these components are to damage from small debris particles in dirty oil.
Main hydraulic valves are particularly susceptible to damage and poor or erratic operation due to the precise fit between spools and valve housings. Spools can be scored or even bind up by particle contamination. Small orifices, passages and seats can also prevent flow or leak from particle contamination, causing hydraulic malfunction.
The plungers in a piston pump or motor are lubricated through small oil passages in each of the pistons. Lack of lubrication from plugged oil passages can result in catastrophic failure. Catastrophic hydraulic component failures contaminate the system with metal shavings that eventually clog the hydraulic return oil filter. Some return oil filters have a filter bypass that opens when filters plug and backpressure gets too high, dumping unfiltered trouble right back to the tank! Once in the tank, contaminated oil gets circulated through the system to cause more damage. What does this all mean for the machine owner? It means reduced component performance, reduced machine production, increased downtime, shorter component life and higher repair costs.
7 Anti-contamination Tips
1. Use recommended hydraulic oils that meet manufacturer specifications and make sure the ISO grade is appropriate for the ambient temperatures encountered.
2. Never add oil through a tank access cover! Hydraulic oil straight from the drum will contaminate the hydraulic system. All oil must be pre-filtered before entering the reservoir.
3. Keep an eye out for plugged filter indicators. When a filter clogs an indicator light warning of higher than normal filter back pressure indicator should illuminate. When this indicator is tripped, inspect and replace filters as soon as possible. Remember, when oil bypasses the filter element, unfiltered oil is being redirected back to tank.
4. When changing filter elements, inspect the oil around the element for metal flakes before removing it. If flakes are present or if there has been a pump or motor failure recently, do not remove the filter element. Doing so will allow the contaminated oil around the element to drain directly into the tank. Remove the entire filter assembly to change the element, this will help contain debris.
5. Clean hoses thoroughly before installation.
6. Replace all components, including hoses, in the cleanest environment possible. Make sure hoses and ports are capped during transportation and before installation.
7. Test the hydraulic fluid for contamination on a regular basis, especially if only one type of oil is used throughout the year.
Article by Kurt Moncini, Marketing Director, Forest Machine Business Department, Komatsu, America Corporation
Latest News
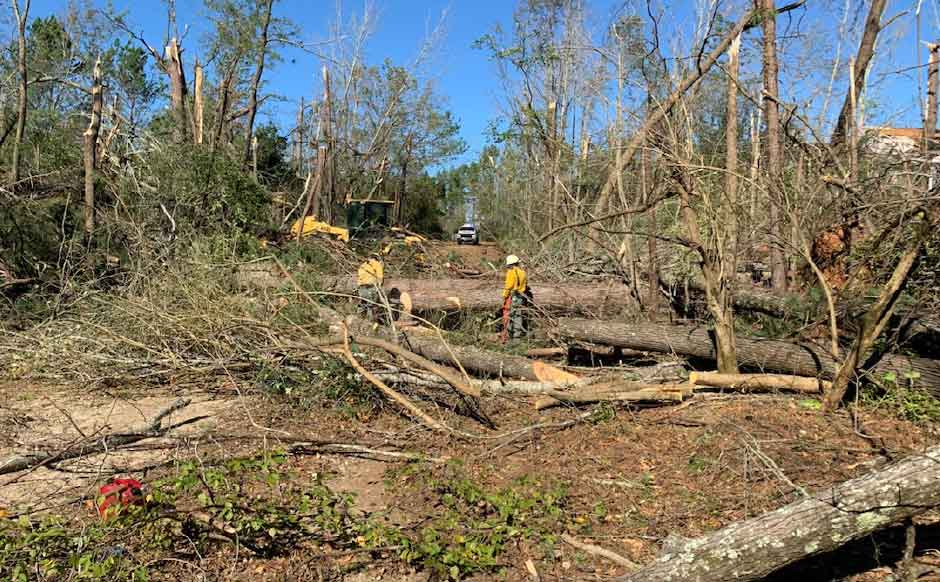
Northeast Texas Tornadoes Cause Estimated $13 Million In Damage To Timber
A series of tornadoes that struck Northeast Texas in early November damaged timber on more than 10,000 acres; the timber was worth an estimated $13 million. Storms that tracked across North Texas on Nov. 4 resulted in seven tornadoes, five of which…

Alabama Wildlife Federation, The Westervelt Co. Unveil “Westervelt Forest”
Representatives of the Alabama Wildlife Federation (AWF) and The Westervelt Co. unveiled “Westervelt Forest” with a ribbon cutting on December 6. The seventy-acre working forest and wildlife demonstration area, located at AWF State Headquarters in…
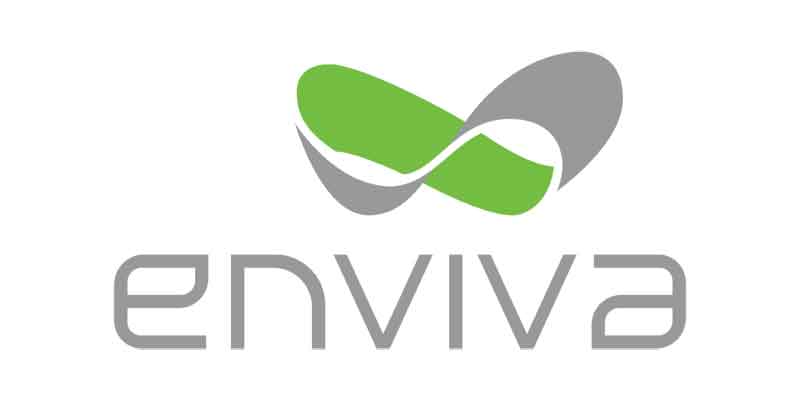
Enviva Plants Longleaf As Part Of NC Forest Restoration Project
Enviva has partnered with the Sandhills Prescribed Burn Assn. and Milliken Advisors to sustainably thin the loblolly pine on over 500 acres of Hoke Community Forest in preparation for the establishment of a longleaf pine savannah in North Carolina….
Have A Question?
Send Us A Message