Keep Hydraulic Hose Contamination In Check
The need for hose replacement is a fairly common occurrence on hydraulic machines. Hydraulic hose fabrication is a big business with plenty of competition and more than a few cowboys running around. So if you own or are responsible for hydraulic equipment, then where you source replacement hoses, and how they’re made, cleaned and stored prior to installation on your machine, warrants your attention.
The hose fabrication process—or more specifically, the hose cutting process—introduces contamination in the form of metal particles from the hose’s wire reinforcement and the cutting blade itself, and polymer dust from the hose’s outer cover and inner tube.
The amount of contamination that enters the hose during cutting can be reduced by employing techniques such as using a wet cutting blade instead of a dry one, blowing clean air through the hose as it is being cut and/or using a vacuum extraction device. The latter two aren’t very practical when cutting long lengths of hose from a roll or in a mobile hose-van situation.
Therefore, the main focus must be on effectively removing this cutting residue and any other contamination that might be present in the hose—prior to installation. The most efficient and, therefore, most popular way of doing this is by blowing a foam cleaning projectile through the hose using a special attachment connected to compressed air. If you are not familiar with this equipment, do a search on Google for “hydraulic hose projectile.”
The manufacturers of these cleaning systems claim that hose cleanliness levels as good as ISO 4406 13/10 are achievable. But like most everything else, the results achieved depend on a number of variables, which include using a projectile of the correct diameter for the hose being cleaned, whether the projectile is used dry or wetted with solvent, and the number of shots fired. Generally, repetitive shots result in cleaner hose assemblies. Furthermore, if it is a new hose that’s being cleaned, the projectile cleaning should be done before the ends are crimped on.
Hose Horror Stories
Almost all hydraulic hose fabricators these days have and use hose cleaning projectiles; but how meticulous they are when doing it is another matter entirely. This means if you want to ensure you take delivery of hose assemblies to a certain standard of cleanliness, it’s something you must specify and insist upon, as the following account from a heavy equipment mechanic demonstrates:
“I was changing some hoses on a Komatsu 300 HD for a customer and he noticed me washing out a hose before I put it on. So he asked: ‘They clean ‘em when they make ‘em, don’t they?’ I said, ‘Sure, but I like to check.’ I took the caps off a new hose and washed it with solvent and emptied the contents into some paper towels as he watched. His response was ‘holy (expletive).’” And it’s not just the standard of the cleaning which must be insisted upon. A few years back I was at a client’s premises when its hose supplier arrived to deliver a big supply of hose assemblies. When the pallet came off the truck, it was obvious that none of the hoses were capped to prevent contaminant ingression. And the customer accepted them! As soon as I saw what was going on, I advised my client to require all hoses be delivered with caps installed and not to accept them otherwise.
Abrasion, Bending
This sort of penny foolishness should not be tolerated from any hose fabricator.
When it is time to install a replacement hose, other than ensuring it’s clean, pay careful attention to routing, ensure all clamps are secure and tight, and if necessary, apply inexpensive polyethylene spiral wrap to protect the hose from abrasion.
Hydraulic hose manufacturers estimate that 80% of hose failures are attributable to external physical damage through pulling, kinking, crushing or abrasion. In fact, abrasion caused by hoses rubbing against each other or surrounding surfaces is the most common type of damage. Another cause of premature hose failure to look out for when replacing a hose is multi-plane bending. Bending a hydraulic hose in more than one plane results in the twisting of its wire reinforcement. A twist of 5° can reduce the service life of a high-pressure hydraulic hose by as much as 70%, and a 7° twist can result in a 90% reduction in service life.
Multi-plane bending is usually the result of poor hose assembly selection and/or routing, but also can occur as a result of inadequate or insecure clamping where the hose is subjected to machine or actuator movement.
Paying attention to these often-overlooked details will not only ensure replacement hoses aren’t responsible for contaminant ingression and possible collateral damage to the hydraulic system they become part of, they’ll last the way they should, too!
Article by Brendan Casey
Casey has more than 20 years experience in the maintenance, repair and overhaul of mobile and industrial hydraulic equipment. This article appeared earlier in Machinery Lubrication. For more information on reducing the operating cost and increasing the uptime of your hydraulic equipment, visit InsiderSecretsToHydraulics.com.
Latest News
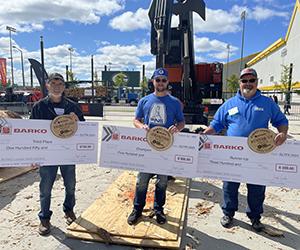
The BARKO Loader Skills Competition 2024
The BARKO Loader Skills Competition, conducted as part of the annual BARKO trade show tour, held the final competition of 2024 at the GLTPA Logging Congress in Green Bay, WI in September. The skill level, competitive atmosphere and the return of...
Virginia Forestry Assn. Seeks Executive Director
The Virginia Forestry Assn. (VFA), a not-for-profit trade association dedicated to representing Virginia’s diverse forestry community and promoting the sustainable use and conservation of forest resources to ensure their long-term benefits for all...
Have A Question?
Send Us A Message